Как делают диски для машин
Опубликовано: 16.05.2024
Если на вашем авто стоят литые легкосплавные диски, вам наверняка будет интересно узнать, как и из чего они производятся. Технология изготовления литых дисков значительно сложнее, чем может показаться на первый взгляд. Значение имеет все: выбор сплава, температуры, способы механической обработки и многое другое.<>/p
Автодиски начинаются с металла
Читая отзывы о литых дисках, вы наверняка обратили внимание на то, что продукция одних брендов вызывает восхищение, а других — всплеск негатива. Качество основы будущих колес во многом зависит от состава сплава. Большинство брендов производит литые диски из прочного сплавов алюминия с добавкой других металлов. Для недорогих моделей обычно используют сплав с добавкой кремния, например, g-AlSi10/11 или g-AlSi7. Они неплохо переносят термическую обработку, проявляют сравнительно неплохую устойчивость к механическим нагрузкам. Для более качественных колес состав сплава несколько другой: основой по-прежнему выступает алюминий, а в качестве добавок выступают магний или титан.
Как это делается? На начальном этапе металлы в форме болванок отправляются в печь, где их разогревают до температуры плавления — 600-700 градусов по шкале Цельсия. Затем расплавленный сплав заливается в форму. Однако не все так просто, ведь производители применяют различные технологии.
Способы литья
-
Чтобы получить отливку, на заводе могут использовать разные методы литья:
- гравитационное (в кокиль);
- с противодавлением.
Выбор способа зависит и от сплава, и от расчетной стоимости дисков (для бюджетной категории часто используют менее дорогостоящие варианты). У каждого метода имеется собственный набор достоинств и недостатков. Если используется гравитационное литье, автоматы заливают в формы алюминиевый сплав при нормальном атмосферном давлении. После остывания получается заготовка с равномерной мелкозернистой структурой. Для магниевых дисков стараются использовать другие методы, поскольку металл приходится разогревать до более высоких температур, и в процессе охлаждения качество оказывается не слишком высоким.
При литье под низким давлением, как понятно из названия, приходится создавать разреженную атмосферу. Это требует дополнительных затрат, но окупается: металла требуется меньше, а отливки получаются на 10-15 процентов прочнее и почти в два раза пластичнее, что непосредственно влияет на дальнейшую обработку и характеристики колес.
Еще более совершенным способом считается литье с противодавлением. На этот раз на заготовку воздействует давление газов, которое приводит к уплотнению сплава и уменьшению количества брака. Диски, изготовленные этим способом, оказываются на 5-10% прочнее отлитых под низким давлением. К тому же, технология позволяет сократить время создания отливки.
Тестирование
Следующий этап, без которого невозможно обойтись, - проверка качества. На современных предприятиях она проводится в автоматическом режиме. Специальное оборудование обнаруживает пустоты и каверны, проверяет плотность заготовок, определяет нарушения заданных размеров. Если в процессе проверки обнаруживается брак, его отправляют на переплавку, так что процент отходов достаточно мал.
В некоторых случаях диски проходят через стадию закалки, чтобы приобрести большую твердость. Нагрев и охлаждение проводят несколько раз, а диапазон температур во время закалки — от 150 до 200 градусов. Однако эта операция может придать сплаву хрупкость, так что при сильном ударе он не согнется, а пойдет трещинами или лопнет.
Окончательная отделка
Поверхность заготовки сильно отличается от готовой продукции, поэтому необходимо убрать с поверхности все лишнее. Для этого будущие диски обтачивают на специальных станках. Фрезы придают болванке форму, после чего проводится повторный контроль качества.
Дальнейшее зависит от выбранного дизайна. Некоторые модели полируют, другие матируют с помощью химической или механической обработки. Отдельные бренды, выпускающие разноцветные яркие колеса для тюнинга, включают в техпроцесс еще одну операцию: окрашивание. На современных предприятиях обычно используют полимерные порошковые краски, которые образуют прочное и равномерное покрытие на спицах или декоративном колпаке. Затем наступает очередь последней проверки, после чего колесные диски поступают на склад готовой продукции, а позже отправляются к официальным дилерам, которые распространяют их по магазинам.
Промышленная индустрия предлагает автомобилистам большое многообразие комплектующих, с помощью которых можно персонализировать транспортное средство и улучшить его технические характеристики, эксплуатационные качества, внешнюю привлекательность. В первую очередь в этом контексте речь идёт о легкосплавных колёсных ободах . Все знают, что алюминиевые или титано-магниевые диски на порядок лучше металлических, но далеко не каждому известно, за счёт чего обеспечивается тотальное превосходство. Прочитав эту статью, вы узнаете, как изготавливают литые диски на Ауди A5 в промышленных масштабах и поймёте, почему штампованными ободами комплектуются только бюджетные автомобили.
Материалы и сплавы
Есть производители, которые используют титано-магниевые (требуют бережной эксплуатации ввиду повышенной хрупкости и особого ухода) и другие экзотические сплавы для производства колёсных ободов, но наиболее востребованными в этом контексте являются алюминиевые разновидности. Эти две вариации с включением кремния: g-AlSi7 и g-AlSi10/11 - самые распространённые. Они обладают оптимальным соотношением прочности к массе и пластичности, благодаря чему улучшается поведение авто на дороге (снижаются неподрессоренные массы, повышается манёвренность, за счёт более эффективного охлаждения надёжнее работают тормоза).
Литьё
Сплав для отливки заготовок большинство производителей получают самостоятельно. Для этого используются тигельные печи, слитки алюминия, кремний и легирующие компоненты. Есть ряд стандартных сплавов, но существуют и особые, точная рецептура которых является коммерческой тайной производителя.
Расплав заливается в матрицы гравитационным способом (самотёком под воздействием силы тяжести) или под низким давлением. Второй способ более распространён ввиду получения заготовки более высокого качества, первый постепенно изживает себя. В качестве альтернативы литью ряд топовых автопроизводителей используют холодную штамповку из алюминиевого сплава, но эта технология не применяется повсеместно.
Механическая обработка заготовок
Из литьевого цеха выходят изделия, в которых вы бы никогда не узнали диски на БМВ X5 . Это заготовки круглой формы, которые превратятся в диски только после качественной фрезерной обработки. Для этого в промышленных масштабах используются станки с программным числовым управлением. Они обрабатывают болванки с точностью до сотых долей миллиметра, создавая рисунок спиц, задуманный дизайнерами. На этом же этапе проделываются отверстия для ступицы и крепёжных болтов.
Декоративная обработка
На этом этапе диски избавляют от зазубрин, заусенцев, их шлифуют и полируют, готовя к следующим этапам и делая поверхности идеально гладкими. Это покраска или хромирование/никелирование и нанесение защитных составов.
Хром и никель наносятся на готовые изделия методом гальваники (толщина слоя измеряется в микронах). Они делают поверхность ободов очень эффектной, придавая ей вид зеркала или амальгамы. Попутно хромирование/никелирование ощутимо повышает антикоррозийные свойства изделия (алюминиевые сплавы не ржавеют, но подвержены окислению).
Покраска ободов осуществляется преимущественно путём применения порошковой технологии. На практике это выглядит так: обода поляризуют (при помощи электричества им придаётся положительный заряд), а затем обсыпают отрицательно заряженной краской в виде порошка. Разнонаправленно заряженные частицы притягиваются, поэтому порошок прилипает к поверхности ободов тонким ровным слоем. После этого они отправляются в печь, где краска спекается, образуя прочное монолитное покрытие.
Нанесение защитных составов - финальный аккорд. Они призваны уберечь краску или гальванические слои от потускнения, истирания, преждевременного износа и сохранить внешнюю привлекательность ободов как можно более продолжительное время.
Проверка качества и безопасности
Это неотъемлемая часть политики любого уважающего себя производителя. Помимо этого торговые марки обязывают сертифицировать свою продукцию, так как от её качества напрямую зависят безопасность и комфорт автовладельцев, устанавливающих на свои авто легкосплавные диски для Porsche Cayenne R20 . Проверки проводятся при помощи технических средств (мощная оптика, ультразвуковые датчики, рентгенологическое оборудование, специальные стенды, имитирующие динамические и статические нагрузки) и визуального контроля продукции. Выборочно некоторые экземпляры могут распиливаться с целью ознакомления с качеством сплава и его техническими характеристиками изнутри. Тестирование продукции осуществляется и на специально оборудованных полигонах производителей. На них воссозданы максимально жёсткие условия (ямы, выбоины, брусчатка, поребрики, канавы, рытвины), с которыми водители могут столкнуться в ходе эксплуатации дисков.
Сайт сдается в аренду - обращайтесь на ipassat@mail
+7 905 688 68 78
Как делают литые диски - секреты производителей
В настоящее время никого не удивить литыми дисками на машине. А ведь лет тридцать назад их можно было назвать роскошью. Эти изделия тогда очень дорого стоили, а поэтому позволить их мог не каждый. Однако прогресс на месте не стоит, и сейчас литые диски пополнили рынки практически до отказа. И для начала им понадобилось напрочь вытеснить штампованные диски, с чем они удачно справились. Как делают литые диски, следует рассмотреть в данной статье.
Рассматриваемые изделия теснят обычные из-за того, что обладают легкостью (сказывается благоприятно на подвеске, нагрузке и расходе топлива) и эстетичностью (достаточно красивые и привлекают внимание, отлично смотрятся на Mitsubishi, Honda, Toyota и других автомобилях). Сейчас есть большой ассортимент литых дисков, различающихся не только по тысячам форм и цветов, но и техническим и геометрическим параметрам.
Из названия следует заметить, что синоним слова «литые» - «льются». А льются они из сплавов алюминия и магния, которые делают изделие прочным к механическим воздействиям. Ранее литые диски производились исключительно из крылатого метала. Из-за этого страдала надежность, что отрицательно сказывалось на репутации. Во многих странах эти диски так и прозвали – алюминиевые. Для того, чтобы придать дискам максимально возможной устойчивости и жесткости к повреждениям (учитывая отечественные дороги), в структуру пришлось добавить именно магний. В итоге получилась достаточно прочная и выносливая конструкция и чтобы ее сломать, придется изрядно попотеть.
Процесс изготовления литых дисков
Процесс производства литых дисков ведет свое начало с болванок металла (магния и алюминия) в требуемой пропорции. Материалы укладываются в специальную печь и нагреваются до 700 градусов по Цельсию. Только при такой температуре металл способен расплавиться. Далее жидкая смесь переливается в подготовленные формы, уже имеющие вид диска. И все же, о хорошо обработанной болванке говорить слишком рано. Следующим этапом является охлаждения диска в воде для придания ему жесткости.
Чтобы литое изделие получило окончательную упругость, его требуется нагреть определенное количество раз, а затем снова остудить. В данном случае температурный диапазон составляет от 150 до 200 градусов. Кстати, здесь диски охлаждают на воздухе.
Далее мастера переходят к обточке диска. Литую болванку следует тщательно обточить и обработать, чтобы получить правильные динамические показатели, заявленные в технических характеристиках.
Болванка закрепляется на специальном стенде, где ее обрабатывают фрезы, гуляя по диску и тем самым снимая фрезу. После завершения данного процесса диск готов к эксплуатации. Его запаковывают и доставляют в магазины.
Следует отметить, что производство литых дисков не несет каких-либо отходных материалов. Ведь стружка, снятая с диска, переплавляется и используется дальше.
Ремонт грузовых автомобилей лучше всего проводить у профессионалов, найти которых можно на в интернете.
В преддверии установки больших тормозов на свою верную подругу (озадачился я поиском кованных колес… А в процессе поиска узнал много нового!
Все мы знаем что литые диски лучше стальных (штампованных), также многие из нас знаю что кованые диски лучше чем литые. Но далеко не каждый знает как куются кованые диски. К сожалению никаких наковален и мехов в этом деле не применяется…
Небольшое видео отступление, в ознакомительных целях. Собственно весь процесс:
Теперь, давайте почитаем статью из журнала «Популярная механика», о том как делают кованые диски.
Мы стоим в кузнечно-прессовом цехе Ступинской металлургической компании, над нами возвышается гигантский пресс, развивающий усилие в 10 000 тонн. Бригада рабочих меняет оснастку штамповочного пресса, а Александр Ловчев, заместитель начальника производства дисков автомобильных и мотоциклетных колес Ступинской металлургической компании (СМК), раскрывает нам секреты производства кованых колес. «Вообще-то ‘кованые’ – это не совсем точно с технической точки зрения, правильнее было бы называть их дисками, изготовленными методом горячей объемной штамповки в закрытых матрицах, – улыбается Александр. – Но столь сложное название с первого раза мало кто способен выговорить, так что слово ‘кованые’ вполне прижилось».
«Эти диски – дальние родственники самолетов, – продолжает Александр. – В начале 1990-х множество предприятий, работавших в советское время на авиацию и космос, с уникальным оборудованием и технологией, оказались без госзаказов. И, чтобы выжить, вынуждены были перейти на товары народного потребления. Кто-то стал делать кастрюли, а СМК – в том числе и колесные диски. Технологии используются действительно самолетные – как при производстве некоторых силовых элементов конструкции планеров». В этом отношении российским автомобилистам повезло: такие прессы есть далеко не во всех странах. А даже где есть – подобное чрезвычайно дорогое оборудование, как правило, работает в основном на авиационно-космическую (а вовсе не на автомобильную) промышленность.
От отливки к колесу
Литейный цех – первый этап любого металлургического производства
Для дисков используется сплав типа АВ на основе алюминия с легирующими добавками магния, меди, меди, кремния и марганца. Он не только высокопрочен, но и пластичен. За рубежом аналог этого сплава обычно называют «авиационный алюминий 6061» (aircraft grade Al 6061). Готовую отливку – цилиндр диаметром примерно 20 см – режут на куски нужной длины (в зависимости от размера будущих колес), складывают в корзины и отправляют в кузнечно-прессовый цех.
Секторный штамп. При горячей объемной штамповке используются вот такие штампы, состоящие из нескольких секторов. При окончательном формировании диска верхняя часть штампа опускается, и сектора сходятся. Излишки металла при этом выдавливаются через щели, образуя облой
Там эти заготовки, пока даже отдаленно не напоминающие колесные диски, разогревают и с помощью пресса «осаживают» – сплющивают, превращая в «блинчики» толщиной сантиметров двадцать и диаметром около полуметра. Процесс дальнейшего превращения в колеса происходит в несколько этапов. Сначала «блинчики» разогревают до 430С и с помощью предварительного штампа (разогретого примерно до 350С) превращают в «кастрюли» – предварительные заготовки для автомобильных колес.
После термообработки колеса ожидают отправки в цех мехобработки
«Кастрюли» вновь отправляются в печь для разогрева, а затем специальный конвейер подает их к прессу с другим установленным штампом – окончательным. «Пауза между выходом заготовки из печи и собственно штамповкой не должна быть больше 11 секунд, иначе заготовка остынет ниже критической температуры», – поясняет Александр. Один из рабочих смазывает разогретый штамп специальной смазкой, двое других ловко хватают «кастрюлю» длинными щипцами и переносят на пресс-форму. Верхняя часть пресса опускается, поднимается – и вот из-под пресса достают готовое, если не считать облоя (излишков материала, выдавленных при штамповке), колесо. Первые четыре отштампованных колеса после освоения нового штампа идут на контроль геометрии – только после этого дается разрешение на использование штампа для серийного производства дисков.
Цилиндрические катки – это заготовки будущих колес для автоспорта
Пресс с усилием в 10 000 тонн (в СМК таких два) позволяет изготавливать диски большого диаметра. «Мы – единственное предприятие в России, кто освоил производство дисков диаметром до 22 дюймов! – с гордостью говорит Александр. – Меньшим усилием их просто не продавить – придется разогревать сплав до почти жидкого состояния, а это уже не объемная, а ‘жидкая штамповка’ – так мы называем литье под высоким давлением».
Термообработка и контроль
Несмотря на уже проступившее внешнее сходство, механические свойства колес пока еще далеки от тех чудных качеств, которыми славится «ковка». А славится она высокой прочностью (превышает прочность литых дисков при существенно меньшей массе), пластичностью (в отличие от литых дисков, кованые при высоких нагрузках деформируются, а не разрушаются) и упругостью (при умеренных нагрузках они деформируются упруго).
Для получения всего этого как раз и нужна термообработка. Сначала колеса подвергают закалке – равномерно прогревают в течение нескольких часов в печи до 515С, а затем быстро охлаждают, погружая в воду. После закалки сплав уже имеет нужную мелкозернисто-волокнистую структуру, но для того, чтобы колеса приобрели нужные механические свойства, их нужно «состарить» – подождать, пока структура выровняется, и убрать внутренние механические напряжения. В обычных условиях на это может уйти пара месяцев, но, чтобы не терять время, заготовки искусственно состаривают: выдерживают в печи при температуре 150–160С примерно 12–14 часов, после чего медленно охлаждают.
Один из рабочих с помощью кисти смазывает штамповую оснастку специальной смазкой, чтобы готовая деталь не прилипала к пресс-форме
После термообработки не менее 10% заготовок из каждой партии подвергаются контролю. Их поверхность протравливают: на светлой травленой поверхности хорошо заметны дефекты штамповки и складки. А одно колесо из партии безжалостно распиливают, вырезая из него специальный фрагмент – так называемый шаблон. Шаблон шлифуют и протравливают, а затем тщательно изучают в лаборатории на наличие дефектов деформации, термообработки и однородности сплава. «Чаще всего дефекты встречаются в ступичной части, – поясняет Александр. – Там наиболее сложный с металлургической точки зрения характер деформаций и термических нагрузок». На этом этапе также проводится контроль механических свойств сплава – образцы закрепляются в специальной разрывной машине, с помощью которой определяется предел прочности, предел текучести, относительное удлинение и твердость. Если дефекты и значения характеристик материала не укладываются в допуски, изучению подвергается еще одно колесо из партии. Если же и повторная проверка подтверждает эти выводы, значит, имело место нарушение технологической цепочки – и вся партия бракуется. Если же все параметры в норме – партия колес уходит на механическую обработку.
Сделано в России
С заготовки, уже напоминающей по форме будущее колесо, на токарном станке снимают лишний припуск металла, в ободе просверливают ниппельное отверстие, а в ступичной части – крепежные отверстия под болты. Затем колесо устанавливают на фрезерный станок с ЧПУ, который и вырезает запрограммированный дизайн.
«Есть ли ограничения по дизайну? В общем-то, нет – рисунок может быть любым, колесо можно сделать очень легким и ажурным, и единственное ограничение связано с нагрузкой, которую оно должно выдерживать, – отвечает на мой вопрос Александр. – Вот, например, этот 15-дюймовый диск весит чуть больше 5 кг, почти в два раза меньше стального штампованного аналога. И при этом параметры его значительно превосходят требования российского ГОСТа. Кстати, такая масса не является рекордной – в свое время мы сделали для японского рынка самое легкое в мире 15-дюймовое колесо – оно весило 3950 г».
Практически готовое колесо – остается только слесарка и покраска
«Некоторые диски после механической обработки дополнительно полируются. Для дисков марки M&K, которыми представлен наш премиум-сегмент, эти операции производятся за рубежом, – продолжает Александр. – Для остальных проводится обычная слесарная обработка – снимаются острые кромки, а затем производится окончательный контроль на соответствие геометрических размеров чертежу, биения обода и дисбаланс.
Последний параметр по ГОСТу контролировать необязательно, но мы это делаем, причем наш ‘внутренний’ стандарт в этом отношении в два раза более жесткий, чем российский ГОСТ. В СМК вообще очень строгая и хорошо налаженная система контроля качества – сказывается авиационное прошлое: на каждом этапе, от отливок до готового колеса, детали отслеживаются по маркировке. Видите, на колесе выбит номер? После покраски, окончательной проверки и одобрения ОТК колесо упаковывают, а его заводской паспорт будет храниться у нас еще в течение десяти лет. Сколько времени занимает производство диска? Около недели чистого времени, но, если учитывать производственный график, получается около месяца».
Российские технологии в области изготовления кованых колес вполне признаны и за рубежом. «В прошлом году на немецком ‘Мотор-шоу’ в Эссене, главной европейской ежегодной выставке в сфере тюнинга автомобилей, несколько тюнинговых ателье выставили очень дорогие машины – Bentley и Aston Martin – именно на наших дисках M&K», – говорит Александр. «А посетители знали о том, что эти диски российские?» – спрашиваю я. «Да, конечно! Клейма ‘Сделано в России’ мы не стесняемся. Мы им гордимся».
К слову сказать в России довольно много производителей кованных дисков, но у них есть один большой недостаток, который объясняется экономической составляющей. Недостаток этот – дизайн, а точнее практически полное его отсутствие.
Посмотрите на диски ВСМПО, хорошие диски, но дизайн сильно на любителя.
Посмотрите на Slik — очень мало дизайнов…
И такая ситуация практически у всех производителей ковки.
Дело немного поправило ателье AGFORGED, ребята договорились с СМК (или Магалтек?), делают дизайн и на заказ, можно сказать в штучном варианте делают диски для всех желающих. Минус такого подхода один – довольно продолжительное время необходимое на изготовление заказа.
Но и их выдавила штука под названием Жизнь. Завод СМК прекратил своё существование, а АГ не имели свои производственные мощности… В итоге все наработки достались Solomon Alsberg`y…
Если верить пользователю VITALIY8 , то в РФ на сегодняшний день остаётся один производитель кованых дисков — КРАМЗ, их поковки использует СЛИК.
Ссылки на сайты производителей.
AGForged: — Дизайн AG на мощностях Solomon Alsberg
Магалтек: magaltech.su
SLIK: />M&K mk-wheels— Делались на заводе СМК
Vindeta: — Завод Авангард
SOLOMON ALSBERG:
Полезный сайт со сводной таблицей веса различных моделей дисков
Вот еще немного видео в тему:
Как делают составные диски
Особенности и технология производства кованых автомобильных дисков
Кованные диски производятся с использованием специализированных методик, которые не в полной мере соответствуют названию изделий. Ковка в классическом понимании не используется, обработка металла осуществляется без деформации с применением молота и наковальни.
Производство начинается с формирования заготовки, которая включает различные металлы и сплавы. Основу составляют: алюминий, марганец и магний. Далее следует несколько производственных этапов:
- нагрев заготовки, доведение металла до пластичного состояния. Температура при этом не превышает 450° C;
- прессование с применением специализированных форм. Так обеспечивается равномерное воздействие на поверхность металла;
- термическая обработка или закалка, которая делает сплавы более твердыми за счет изменения структуры кристаллической решетки;
- проведение механической обработки на токарных и фрезерных станках для устранения шероховатостей, придания металлу однородной структуры.
Некоторые модели дополнительно покрываются краской. В основном производители (преимущественно отечественные) оставляют натуральную металлическую структуру.
В реальности технологию производства дисков правильнее назвать горячая штамповка. Она обозначается словом «FORGED», которое выштамповано на внутренней или внешней стороне диска. Литые аналоги обозначаются, как «CAST» и такая маркировка выпуклая. Это поможет выбрать нужную модель, так как литые и кованные образцы внешне не имеют существенных различий.
Ознакомиться с моделями и ценами на кованые диски можно в нашем каталоге. Если возникнут вопросы, то звоните и наши специалисты дадут бесплатную консультацию.
Преимущества и недостатки кованых дисков
- используемые в производстве сплавы и металлы, устойчивы к воздействию влаги, других негативных разрушающих факторов окружающей среды. Поэтому диски не требуют специального ухода, периодического обслуживания, десятилетиями сохраняют привлекательный внешний вид;
- небольшой вес снижает нагрузку на ходовую часть авто, что в долгосрочной перспективе дает ощутимый эксплуатационный, экономический эффект;
- сохранение целостности покрышки при попадании колеса в яму. В таких ситуациях литые аналоги приводят к образованию боковых порезов.
Что касается цены, то дорого стоят изделия выпущенные за рубежом. Тут играет роль специфика производства, транспортные расходы. Российские заводы поставляют на рынок более дешевую продукцию, которая уступает зарубежным аналогам только менее презентабельным внешним видом. В основном, выпускают кованные диски отечественные оборонные предприятия, располагающие соответствующим оборудованием.
Критерии подбора дисков – какие параметры нужно учитывать
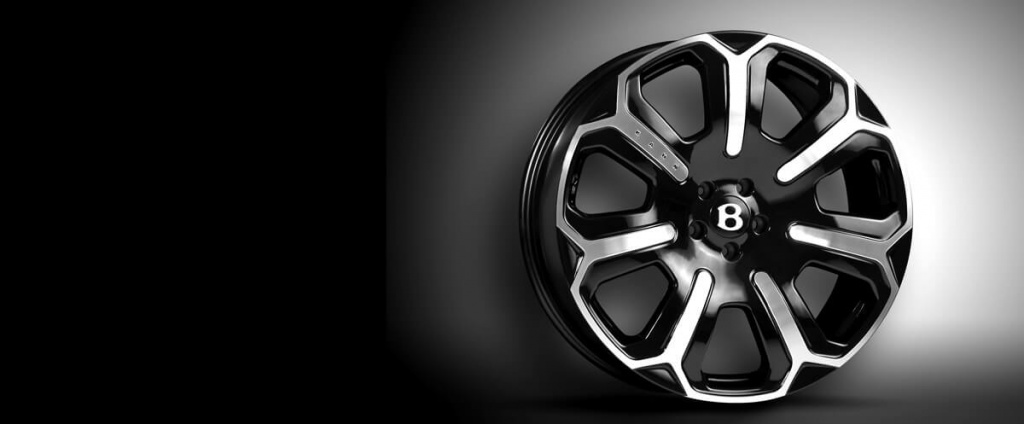
Подобрать диски, которые гармонично впишутся в экстерьер автомобиля, подарят комфорт управления, практичность обслуживания помогут такие параметры.
Посадочный диаметр
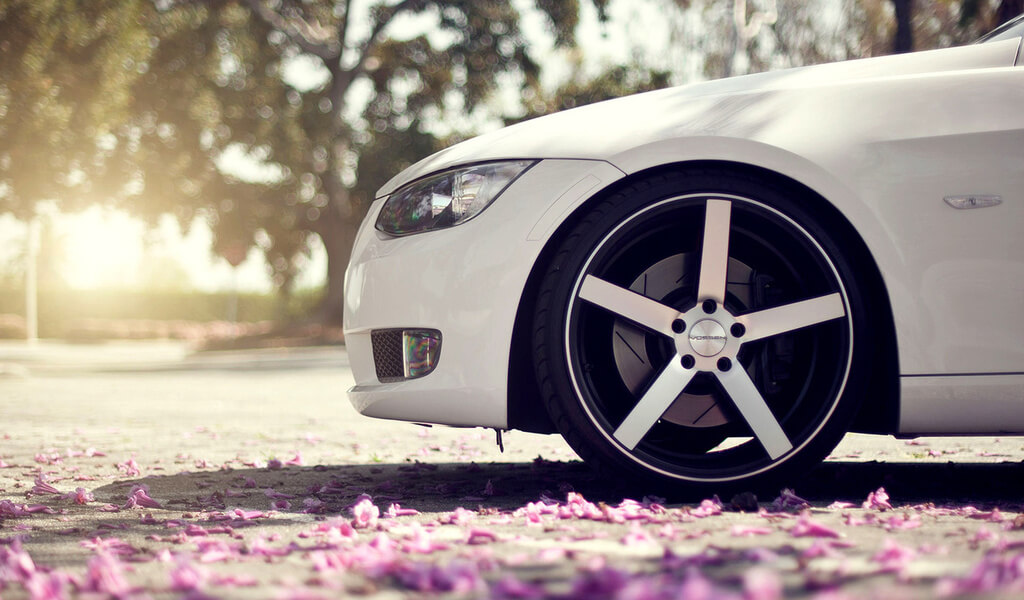
Монтажный или посадочный диаметр – величина измеряется в дюймах, важна для выбора покрышки, также влияет на ходовые характеристики автомобиля.
Ширина

Ширина – параметр обозначается буквой «J», выражается в дюймах влияет на выбор резины. Тут стоит отметить, что ширина шин измеряется в миллиметрах и для правильного выбора стоит использовать специальные таблицы, где указывается соответствие ширины диска и покрышки. Предельно допустимая погрешность не должна превышать 1–2 дюйма. Например, для диска шириной 6 дюймов подойдет резина с типоразмерами, начинающимися со значений 185, 195 мм.
Крепежные отверстия
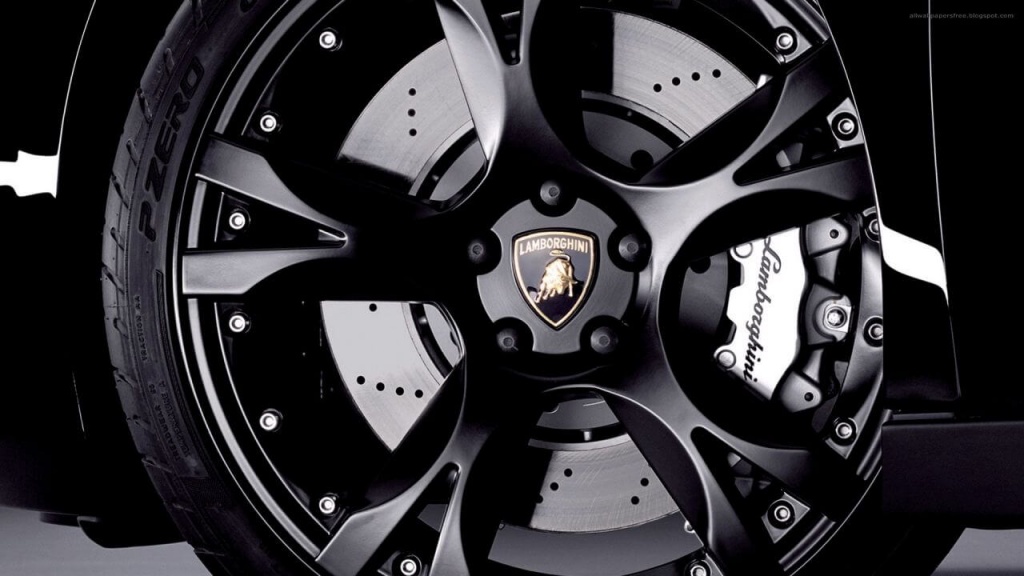
PCD – расположение, количество крепежных отверстий или разболтовка определяется весом автомобиля. В среднем это 4–6 штатных мест для гаек или болтов. Расстояние между ними должно соответствовать аналогичному показателю ступицы автомобиля. Погрешность в несколько миллиметров нельзя компенсировать утягиванием крепежного элемента. Отсутствие центровки приводит появлению биения, неравномерному износу резины, необходимости корректировки настроек развала/схождения.
Форма крепежных отверстий
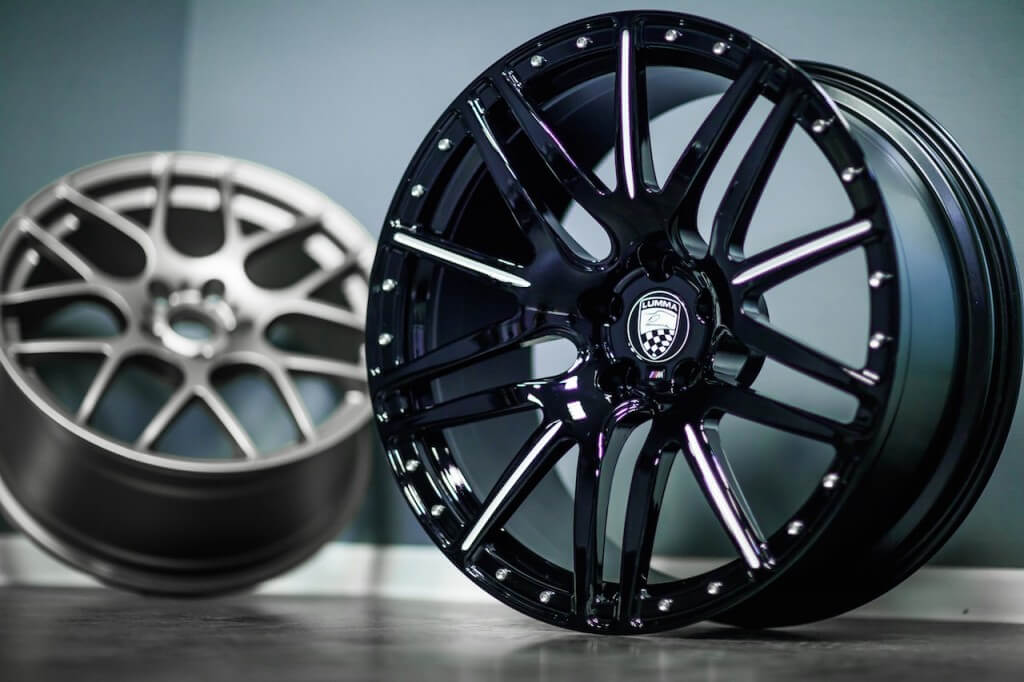
Форма крепежных отверстий – параметр отвечающий за надежную фиксацию диска, плотное прилегание к ступице. У кованных дисков это перевернутый конус или прямая цилиндрическая форма. Категорически запрещено использовать гайки и болты другой формы и длинны. Это чревато авариями, появлением посторонних шумов, снижением комфорта управления автомобилем.
Диаметр центрального отверстия
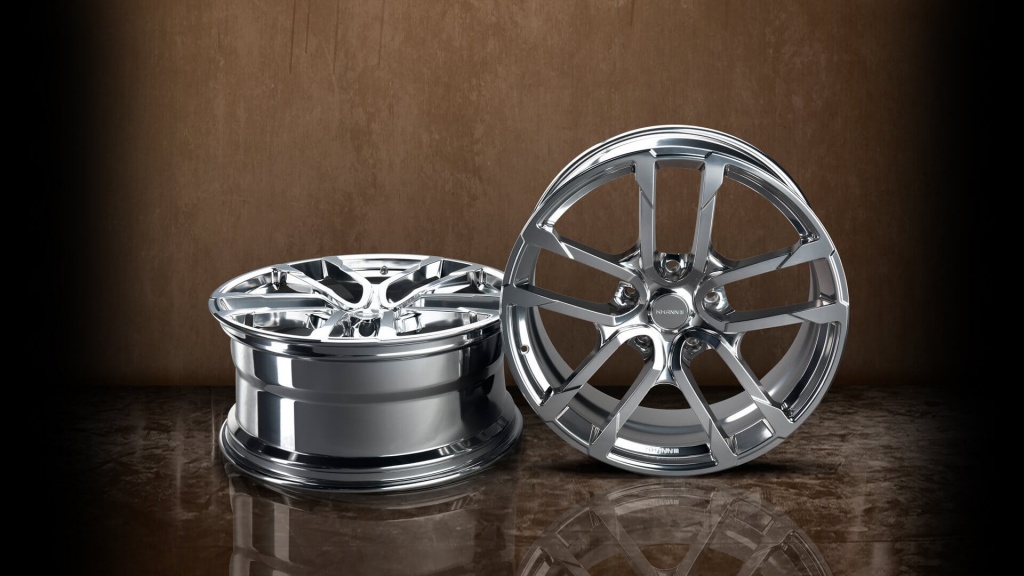
Диаметр центрального отверстия – параметр влияющий на центровку и посадку диска на ступицу колеса. Меньший параметр не позволит его установить, больший, – создаст такие же проблемы, как и при несоблюдении требований к параметрам разболтовки. Для компенсации зазора между диском и ступицей используются пластиковые кольца, которые продаются в комплекте с дисками.
Вылет диска
Вылет диска – геометрический параметр, определяющий расположение диска в колесных арках. Это расстояние между вертикальной плоскостью симметрии колеса и плоскостью приложения диска к ступице измеряется в миллиметрах.
Для правильного выбора, тут необходимо знать, какие бывают варианты:
- нулевой;
- положительный;
- отрицательный.
Изменение вылета влияет на ширину колесной базы, а соответственно, и на габариты автомобиля. Смещение параметра, смещает рулевую ось, что меняет на поведение системы управления.
Хампы
Хампы – бортики, обеспечивающие герметичность при посадке покрышки на диск. Эти элементы есть у всех современных моделей. Они отсутствуют только на изделиях, ориентированных под установку камерных покрышек, которые применяются преимущественно на ретро автомобилях. Работа хампов становится видна при хлопках и ударах по диску во время накачивания воздухом покрышек.
Параметры, характеристики кованных дисков указываются в сопроводительной документации. Они должны соответствовать, не превышать допустимых показателей, указанных производителем транспортного средства. Несоответствие параметров обуславливает необходимость переработки конструкции кузова автомобиля, негативно сказывается на динамике, ходовых характеристиках.
Особенности подбора шин к диску
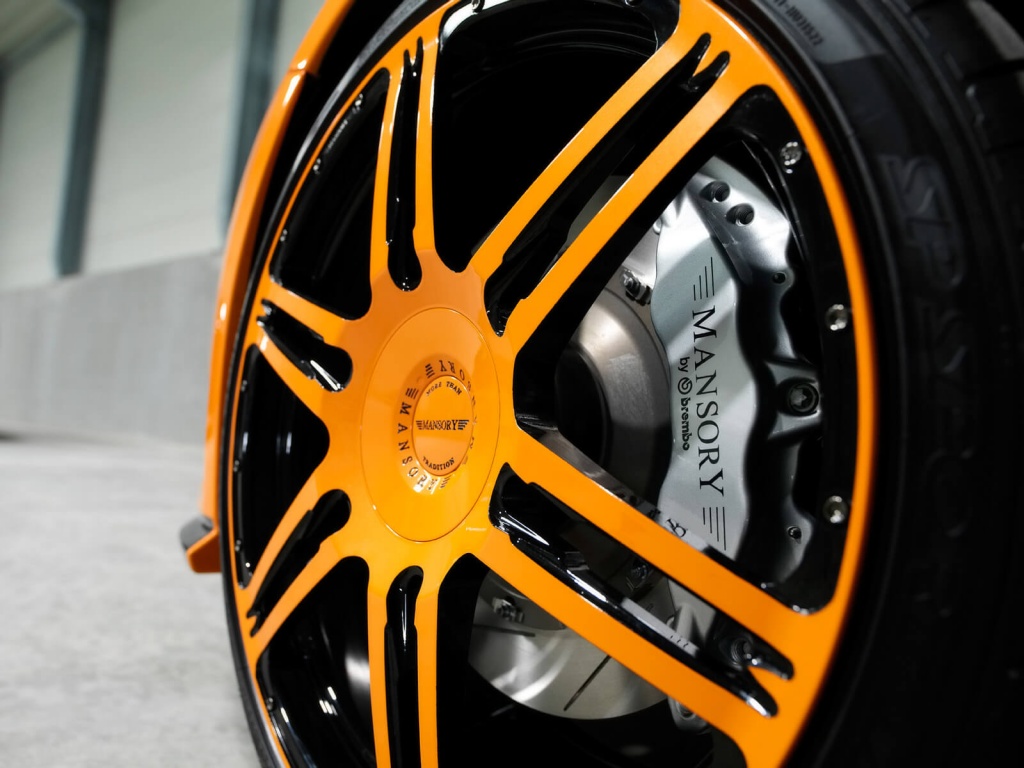
Правильно покупать диски, а к ним подбирать резину. Так обеспечивается комфорт обслуживания и эксплуатации комплекта, исключаются технические проблемы при ремонте, сезонной смене резины.
Важно учитывать совокупность параметров технических и геометрических. Ошибочно ориентироваться только на посадочный диаметр. Но и от него напрямую зависят эксплуатационные характеристики. Тут для правильного выбора, следует ориентироваться на рекомендации производителя авто. Не следует устанавливать диски больше установленного размера. Тут оптимальным решением станет диаметр на 1 дюйм меньше максимального значения.
Подходящая ширина определяется с помощью специальных таблиц или подбирается продавцом-консультантом. Этот параметр, как и вылет диска важен для отсутствия трения шины об подкрылки при максимально вывернутом руле. Форма крепежных отверстий – важный геометрический параметр, если требуется замена крепежных элементов при утере или поломке штатных образцов.
Разболтовка избавляет от проблем с установкой дисков. Но желательно примерять их на месте, чтобы в последствии не терять время на возврат, выбор новых моделей. Так проверяется соответствие диаметра центрального отверстия. Обязательно учитывается вылет диска для сохранения исходных габаритов машины, характеристик рулевого управления.
Знание параметров поможет быстро подобрать колесные диски, которые станут функциональным гармоничным дополнением технической составляющей, украшением дизайна. Полностью надеяться на продавцов не стоит, необходимо разбираться в геометрических и технических характеристиках.
Какую модель выбрать в части дизайна определяет владелец авто, но на первом месте стоят геометрические, технические параметры.
Читайте также: